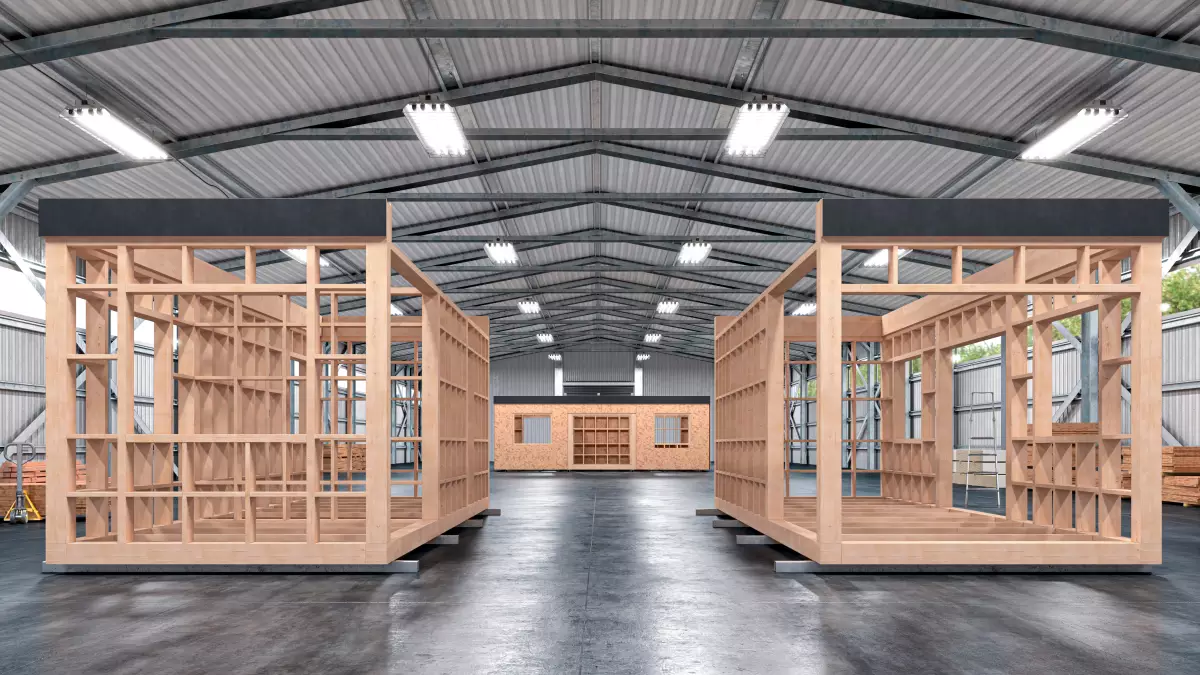
La construction hors-site : un nouveau modèle d'immobilier durable
Alors que l'urgence climatique et la crise du logement imposent une révision des pratiques du secteur de la construction, de nouvelles méthodes émergent pour répondre aux défis de durabilité et d'efficacité. Le secteur du bâtiment reste, en France, l'un des principaux contributeurs aux émissions de gaz à effet de serre et génère d'importantes quantités de déchets. Les règlementations se durcissent pour réduire l'empreinte environnementale, mais les solutions traditionnelles montrent leurs limites. C’est dans ce cadre que la construction hors-site se positionne comme une alternative prometteuse.
Basée sur la préfabrication en usine de modules, cette méthode permet d'assembler rapidement les bâtiments sur site, tout en optimisant l'utilisation des matériaux et en limitant les nuisances liées aux chantiers. Ce procédé connaît un regain d'intérêt, notamment pour sa capacité à produire plus vite, avec une meilleure maîtrise des coûts et un impact réduit sur l'environnement.
Avec le hors-site, chaque étape, de la conception à l'assemblage, est pensée pour maximiser la performance et la durabilité.
Nous verrons ici comment la construction hors-site s'affirme comme un modèle innovant et durable, en détaillant ses avantages, ses défis, et son potentiel pour transformer le paysage immobilier français. Nous reviendrons ensuite sur l’exemple de Nantes, où la construction hors-site est expérimentée comme une solution efficace pour accélérer la production de logements tout en respectant des normes environnementales strictes.
La construction hors-site : une réponse efficace aux défis environnementaux
Selon les données de la Stratégie Nationale Bas Carbone (SNBC), le secteur de la construction représente près de 25 % des émissions de gaz à effet de serre en France. Cette situation est en grande partie due à l’utilisation massive de matériaux tels que le béton, l’acier et l’aluminium, ainsi qu’à des procédés de construction qui génèrent une quantité importante de déchets. Face à ces enjeux, la construction hors-site se présente comme une alternative innovante pour réduire l'empreinte écologique des bâtiments.
Réduction de l'empreinte carbone
En fabriquant les composants des bâtiments en atelier, il est possible d'optimiser l'utilisation des matériaux et de réduire les déplacements des ouvriers et des machines sur le chantier. Cette approche permet de diminuer fortement le recours aux transports, qui représentent une part importante des émissions dans la construction traditionnelle.
De plus, le hors-site favorise l’utilisation de matériaux plus durables et moins énergivores. Par exemple, les modules préfabriqués en bois offrent une alternative intéressante au béton, dont la production est particulièrement polluante. Les constructions en bois permettent également de stocker le carbone pendant toute la durée de vie du bâtiment, contribuant ainsi à atténuer le changement climatique.
Optimisation des ressources et réduction des déchets
La production en usine offre un contrôle précis des quantités de matériaux utilisés, réduisant ainsi le gaspillage. Contrairement aux chantiers classiques, où la découpe et le façonnage des matériaux sur place génèrent une grande quantité de déchets, la préfabrication limite les pertes en réutilisant les chutes ou en recyclant les excédents.
En outre, la construction hors-site facilite l'intégration de principes d'économie circulaire. Certains modules peuvent être démontés et réutilisés, permettant une seconde vie aux matériaux. Par exemple, les panneaux modulaires utilisés pour les façades ou les cloisons intérieures peuvent être récupérés pour de nouveaux projets, contribuant ainsi à une réduction des déchets de construction ET de démolition.
Amélioration des performances énergétiques
En usine, les éléments préfabriqués sont assemblés avec une précision qui garantit une meilleure étanchéité à l’air et une isolation optimale. Ce qui réduit les besoins en chauffage et en climatisation.
De plus, cette méthode permet d’intégrer plus facilement des solutions techniques avancées, comme les panneaux solaires ou les systèmes de récupération d’eau de pluie, dès la phase de conception. La préfabrication offre également la possibilité de tester et de valider les performances thermiques et acoustiques des modules avant leur installation.
La préfabrication comme levier d'innovation
La construction hors-site, bien que perçue comme une méthode récente et innovante, trouve ses racines dans la tradition de la préfabrication. Cette méthode, largement utilisée dans les années d'après-guerre pour faire face à une pénurie de logements, revient aujourd'hui sur le devant de la scène. Cependant, loin des images de bâtiments monotones et de faible qualité de l’époque, la préfabrication se réinvente grâce aux avancées technologiques et à une meilleure organisation des processus.
Ce renouveau est en grande partie porté par des concepts modernes comme le DfMA (Design for Manufacturing and Assembly), qui révolutionnent la manière de concevoir et de réaliser les projets.
Retour sur l'histoire de la préfabrication en France
La préfabrication a connu un essor considérable en France après la Seconde Guerre mondiale. Dans un contexte de reconstruction massive, elle a permis de construire rapidement des milliers de logements. À l'époque, des systèmes comme le procédé Camus ont marqué le paysage urbain avec des ensembles d'immeubles fabriqués à partir de panneaux de béton préfabriqués. Ces méthodes, bien qu'efficaces, ont souvent été associées à une standardisation excessive et à des défauts de qualité, ce qui a terni l'image de la préfabrication.
Dans les décennies suivantes, la préfabrication a été délaissée au profit de méthodes plus traditionnelles. Ce n'est qu'à partir des années 2010 que l'intérêt pour elle a été ravivé, grâce à la prise de conscience des enjeux environnementaux et à l'introduction de nouvelles technologies numériques. Aujourd'hui, la préfabrication s'appuie sur des processus plus sophistiqués, intégrant une conception optimisée et un assemblage de haute précision.
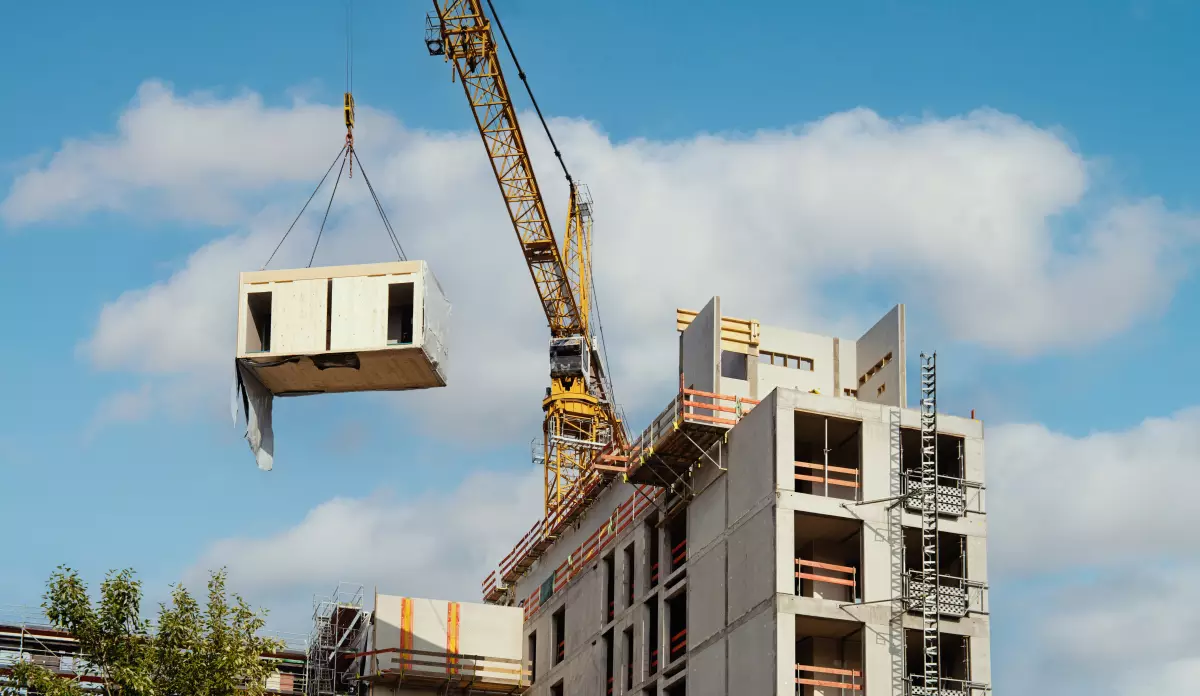
Le DfMA : une méthode révolutionnaire
Le DfMA, acronyme de “Design for Manufacturing and Assembly”, incarne cette nouvelle ère de la préfabrication. Ce concept, qui signifie "conception pour la fabrication et l'assemblage", transforme profondément la manière de concevoir les bâtiments. Contrairement à la construction traditionnelle où le chantier est le point central, le DfMA met l'accent sur la préfabrication dès les premières étapes de conception.
Grâce au DfMA, les architectes et les ingénieurs anticipent les contraintes de fabrication en usine, ce qui permet de rationaliser la production des éléments du bâtiment. Chaque composant est conçu pour être facilement assemblé, avec un minimum de manipulations sur le chantier. Cela permet de réduire les erreurs et d’optimiser les coûts et les délais de construction. Un exemple emblématique est celui des salles de bain préfabriquées : tout, des finitions aux installations sanitaires, est décidé en amont, ce qui élimine les incertitudes et garantit une qualité constante.
Le DfMA s’accompagne souvent de l’utilisation du BIM (Building Information Modeling), qui permet de modéliser en 3D l’ensemble du bâtiment. Cette maquette numérique facilite la coordination entre les différents acteurs et assure un suivi précis du projet. Elle permet également de simuler le montage sur chantier, d’anticiper les éventuels problèmes et d’ajuster les plans avant le début de la fabrication.
L'impact de la préfabrication sur la qualité et l'efficacité
La renaissance de la préfabrication grâce au DfMA et au BIM a permis d'améliorer significativement la qualité des constructions. Les éléments fabriqués en usine bénéficient de conditions de production optimales : contrôle de l'humidité, température stable, précision des outils de découpe et d'assemblage. Ces conditions permettent d'atteindre une qualité difficilement reproductible sur un chantier classique.
De plus, la préfabrication réduit considérablement les délais de construction. Les modules étant préparés en parallèle du chantier, le temps nécessaire pour assembler le bâtiment sur site est réduit à quelques semaines, voire quelques jours pour les structures plus simples. Par exemple, la construction d'un immeuble de logements en modules préfabriqués peut être achevée en moins de trois mois, contre plus d'un an pour une construction traditionnelle.
Cette rapidité et cette efficacité attirent de plus en plus d'acteurs du secteur, qui voient dans la préfabrication un moyen de répondre aux contraintes de coûts et de temps tout en garantissant une haute qualité architecturale. En combinant les atouts de la préfabrication traditionnelle avec les technologies numériques, la construction hors-site ouvre la voie à une nouvelle ère pour le secteur du bâtiment, où innovation et durabilité vont de pair.
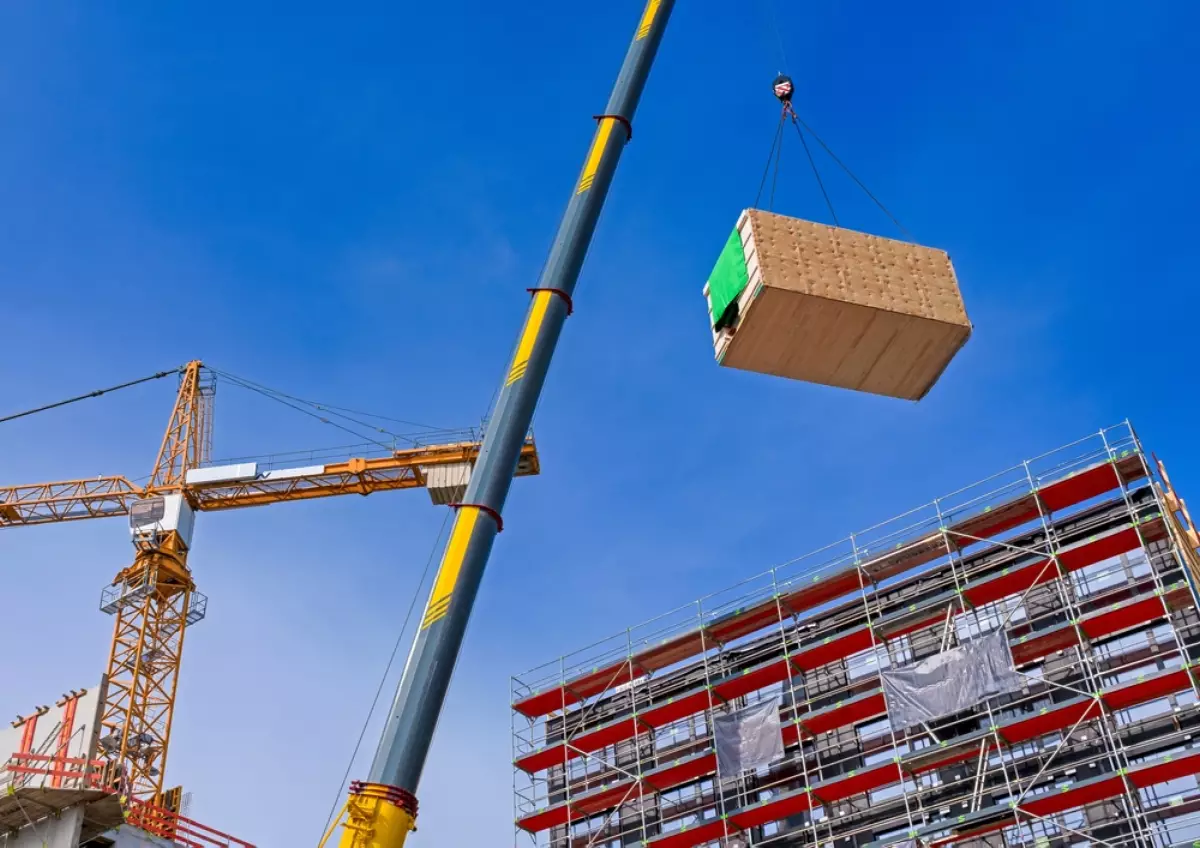
Des avantages économiques et humains
Amélioration des conditions de travail sur les chantiers
Le hors-site représente également un gain important pour les travailleurs du bâtiment. En déplaçant une grande partie des opérations de construction en atelier, dans un environnement contrôlé, on réduit la pénibilité des tâches réalisées sur le chantier. Les ouvriers évoluent dans des conditions plus sûres, mieux protégés des intempéries, des risques liés à la hauteur ou à la manipulation de charges lourdes.
Cette organisation en usine favorise aussi une meilleure gestion des ressources humaines. Le travail en équipe, la répétition des tâches et l’utilisation d’outils plus précis et automatisés augmentent la productivité et la qualité des ouvrages, tout en réduisant les risques d’accidents et les maladies professionnelles.
Les conditions de travail sur le chantier, plus courtes et moins exigeantes physiquement, permettent également d'attirer et de retenir davantage de main-d’œuvre qualifiée dans un secteur souvent confronté à des difficultés de recrutement.
Des coûts réduits et une accession facilitée
La construction hors-site s’affirme aussi comme une solution pertinente pour répondre aux besoins croissants de logements accessibles. En raison des coûts de construction réduits, les logements réalisés par cette méthode peuvent être proposés à des prix plus compétitifs. C’est un avantage déterminant dans des contextes où la crise du logement atteint des niveaux critiques.
Par ailleurs, la flexibilité offerte par cette méthode permet de mieux s’adapter aux contextes urbains contraints. Les modules préfabriqués peuvent être utilisés pour des surélévations d’immeubles, la transformation d’espaces inutilisés ou encore la construction d’habitations temporaires. Ces solutions permettent d’optimiser l’utilisation du foncier en milieu dense comme cela est de plus en plus recherché dans les grandes métropoles qui veulent limiter l’artificialisation des sols et économiser le foncier.
Construction hors-site : Un modèle qui a tout de même ses limites
Si cette méthode suscite un intérêt croissant, elle se heurte encore à des obstacles d’ordre technique, logistique, réglementaire et culturel. Pour que ce modèle devienne une norme dans le secteur du bâtiment, il est nécessaire de surmonter ces limitations et de favoriser une adoption plus large par les professionnels du secteur.
Un risque de standardisation et qualité architecturale
L’un des principaux défis de la construction hors-site réside dans la perception de standardisation. Historiquement, la préfabrication a souvent été associée à des bâtiments monotones et peu esthétiques. Les exemples des grands ensembles construits dans les années 1950 et 1960, avec leurs façades uniformes et leur faible qualité architecturale, continuent de hanter l’imaginaire collectif.
Aujourd’hui, bien que les techniques se soient largement améliorées, le risque de produire des bâtiments similaires reste un frein à l’acceptation du hors-site par les architectes et les urbanistes.
Pour éviter cet écueil, il faut favoriser une collaboration étroite entre les différents acteurs dès la phase de conception. Les architectes, les ingénieurs et les fabricants doivent travailler ensemble pour développer des solutions modulaires qui respectent les spécificités architecturales et le contexte local.
L'utilisation d'outils numériques comme le BIM permet de personnaliser les modules tout en garantissant leur compatibilité avec le processus de fabrication. Des initiatives comme la certification QB Modulaire, qui garantit la qualité et la diversité des constructions hors-site, sont également indispensables pour rassurer les maîtres d’ouvrage et les promoteurs.
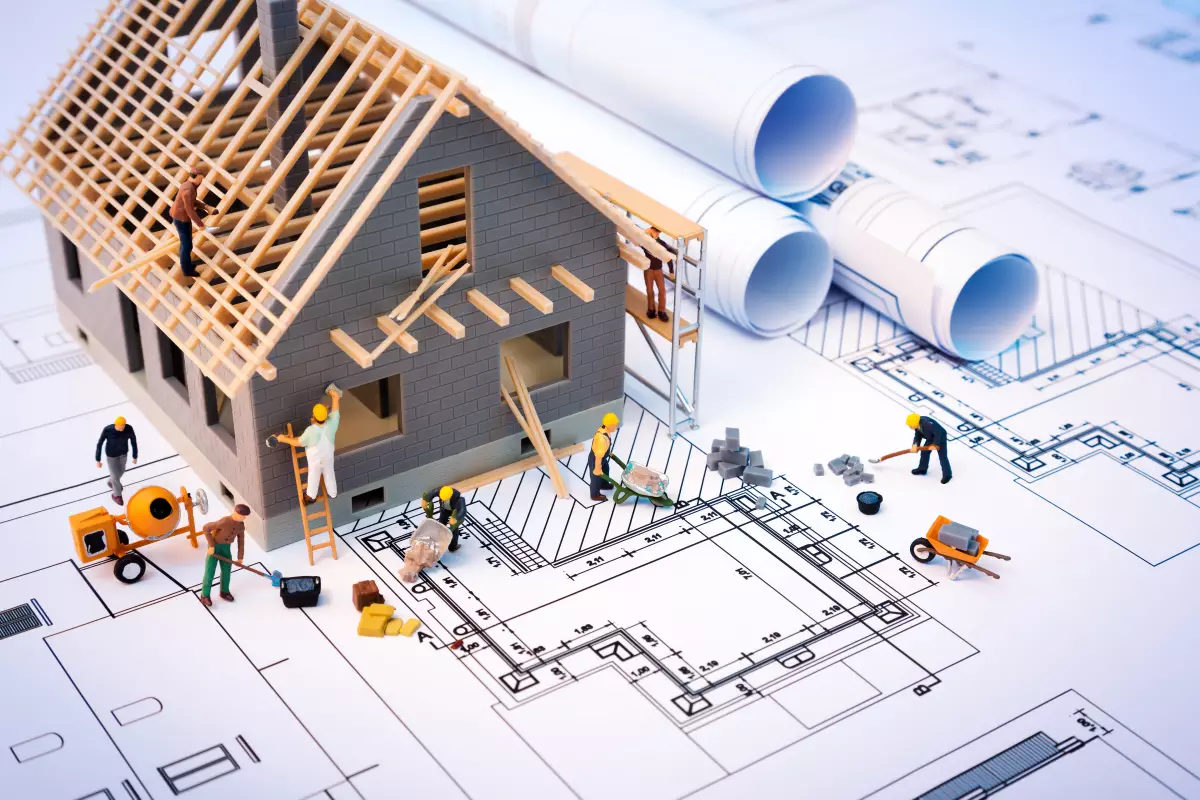
Complexité logistique et gestion de la chaîne d'approvisionnement
Les modules préfabriqués doivent être transportés du site de production jusqu’au chantier, parfois sur de longues distances, ce qui nécessite une coordination minutieuse pour éviter les retards et les surcoûts. De plus, l’acheminement de ces éléments volumineux sur des routes étroites ou dans des zones urbaines denses peut poser des problèmes d’accessibilité et de nuisances.
La construction hors-site repose sur un nombre limité de fournisseurs spécialisés capables de produire des modules de haute qualité. Or, ces entreprises sont encore peu nombreuses en France, et leur capacité de production reste limitée. Cela crée un goulot d'étranglement qui peut ralentir le développement de la filière.
Pour remédier à cette situation, il faut réussir à structurer une véritable chaîne logistique dédiée au hors-site, créant de nouveaux sites de production et en renforçant les collaborations avec les industriels.
Des contraintes réglementaires et normatives
Les normes de construction et les codes du bâtiment sont principalement conçus pour les méthodes traditionnelles, ce qui peut compliquer l’homologation des projets en hors-site. Par exemple, les exigences en matière de sécurité incendie, d’isolation acoustique ou de stabilité structurelle doivent souvent être interprétées de manière plus stricte pour les bâtiments préfabriqués.
En outre, la construction hors-site implique un changement de paradigme dans la manière d’évaluer et de certifier les bâtiments. Les contrôles de qualité doivent être réalisés en amont, dès la fabrication en usine, plutôt que sur le chantier. Un détail supplémentaire qui nécessite une adaptation des processus de vérification et une collaboration accrue entre les bureaux de contrôle, les fabricants et les maîtres d’œuvre.
Le développement de certifications spécifiques, comme celle proposée par le CSTB (Centre Scientifique et Technique du Bâtiment), est une piste à explorer pour faciliter l'intégration du hors-site dans les procédures réglementaires.
Formation et adaptation des métiers
Pour passer à la construction hors-site, les ouvriers et les techniciens doivent acquérir de nouvelles compétences liées à la préfabrication, à l’utilisation des outils numériques, et à la gestion des processus industriels. Or, le secteur du bâtiment, traditionnellement ancré dans des pratiques manuelles, peine à attirer des profils qualifiés dans ces domaines.
Il est donc nécessaire ici de développer des programmes de formation adaptés, en collaboration avec les écoles d'ingénieurs, les centres de formation professionnelle et les entreprises du secteur. La mise en place de cursus spécialisés dans le hors-site, intégrant des modules sur le BIM, le DfMA et les nouvelles techniques de construction, pourrait aider à former une main-d'œuvre qualifiée et à répondre à la demande croissante.
Le développement de la filière en France
L'essor de la construction hors-site en France passe par une structuration de la filière. Des associations comme "Filière Hors-site France" ont vu le jour pour fédérer les acteurs du secteur, qu’il s’agisse des maîtres d’ouvrage, des industriels ou des bureaux d’études.
En outre, plusieurs projets pilotes sont lancés pour démontrer la viabilité de cette approche dans des contextes variés. Par exemple, le groupe 3F, en partenariat avec la Société du Grand Paris et Grand Paris Aménagement, a initié un groupe de travail pour expérimenter le hors-site dans leurs programmes immobiliers. L’objectif est d’atteindre au moins 50 % de constructions neuves réalisées en hors-site d'ici 2031.
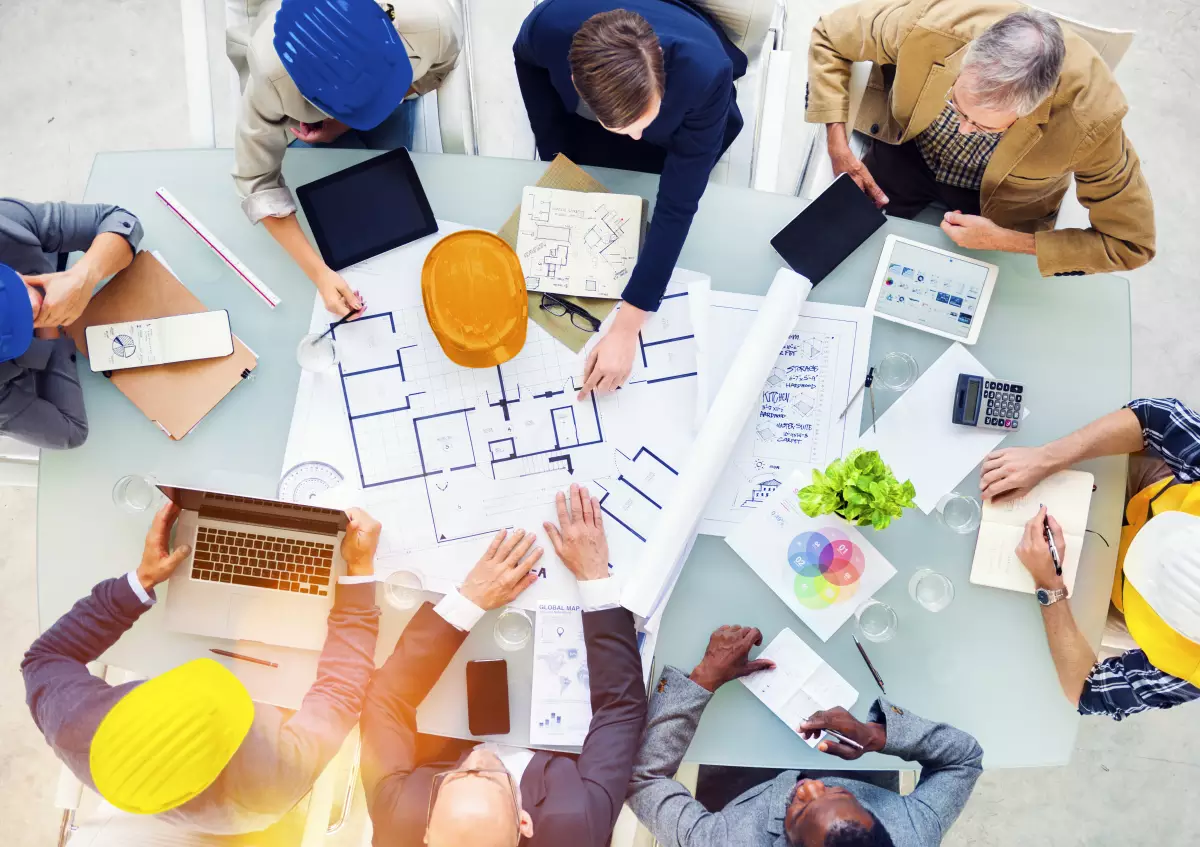
Ce sont ce type d’initiatives qui permettent de visibiliser les bénéfices du modèle et d’identifier les défis à relever pour son déploiement à plus grande échelle. Il faudra également développer l’utilisation de matériaux biosourcés et géosourcés pour instaurer une vraie durabilité de la construction hors-site.
Exemple de Nantes : le hors-site comme solution à la crise du logement
Nantes fait face depuis plusieurs années à une pression croissante sur le marché du logement. La demande dépasse largement l'offre, notamment en matière de logements sociaux. Avec environ 38 000 demandes de logements sociaux en attente, la métropole nantaise illustre les problématiques auxquelles sont confrontées de nombreuses grandes villes françaises.
La ville de Nantes construit en moyenne 900 HLM par an, alors que le PLH en prévoit 2000. Face à cette situation, le hors-site a été adopté comme une solution innovante et efficace pour répondre au besoin de Logements neufs à Nantes.
Une réponse rapide et efficace à la demande de logements
Pour faire face à cette demande urgente, Nantes Métropole a misé sur la construction hors-site afin de réduire les délais de réalisation des projets de logements sociaux. En utilisant des modules préfabriqués, il est possible de construire un immeuble en quelques mois seulement, là où une construction traditionnelle aurait nécessité plus d'un an. Cette rapidité permet de répondre rapidement aux besoins des familles en attente de logement.
La densification urbaine étant un enjeu majeur pour les villes comme Nantes, le hors-site offre des solutions flexibles pour exploiter au mieux les espaces disponibles. La surélévation d'immeubles existants avec des modules légers en bois, par exemple, est une technique qui a déjà été mise en œuvre avec succès.
Les projets actuels construits en hors-site à Nantes
Que ce soit sur des projets déjà construits ou en passe de l’être, Nantes a d’ores et déjà fait appel à la construction hors sol dans plusieurs cas emblématiques.
L’ancienne caserne Mellinet, par exemple, a été réhabilitée et accueille désormais 50 studios du centre d’hébergement pour les sans-abris, qui ont été construits en atelier puis installés sur place.
De même, le projet de résidence pour réfugiés et jeunes actifs du Petit Port est un programme de 100 studios modulaires qui doit être livré d’ici la fin de l’année 2024. Ces studios, préfabriqués en atelier, seront assemblés directement sur le terrain (un ancien parking qui sera réadapté).
D’ici l’été 2025, un autre parking (relais Goudy à Nantes sud) sera réadapté pour accueillir deux nouvelles résidences sociales temporaires, composées également d’habitats modulaires qui seront construits hors-site.